Laser Cooling Solution
Custom the best industrial laser cooling solution with YT Thermal, we provide customers with high efficiency of laser thermal solution designing. Skived fin heat sink or liquid cold plates
Laser Module Coooling Solutions
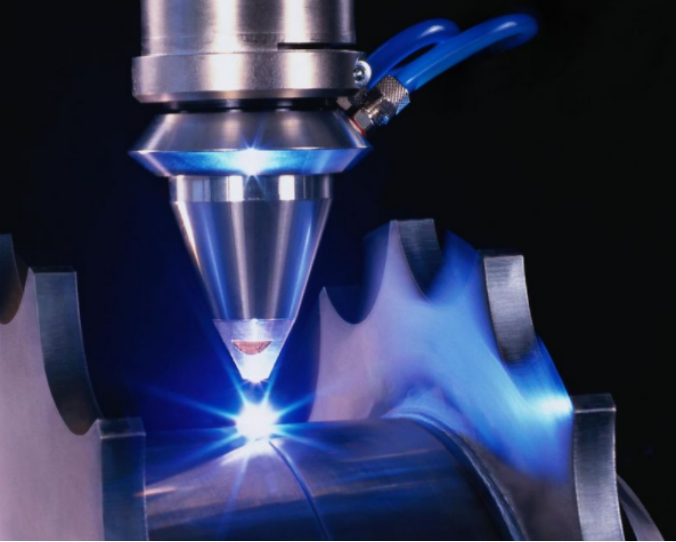
Thermal Solutions for Laser Equipment
The power of semiconductor lasers continues to increase, and the heat dissipation problem caused by it has become a bottleneck restricting the development of semiconductor lasers. The increase in chip temperature causes the performance of lasers to decline. To keep the lasers with good characteristics under high power conditions, it is necessary to strengthen the heat dissipation of the laser chips.
By analyzing the influence of the laser chip temperature on various performance indicators of the laser, the importance of reducing the chip temperature to ensure the normal operation of the laser is explained.
Since the convective heat transfer resistance on the fluid side plays a leading role in the total thermal resistance, the semiconductor laser is mainly analyzed. The heat dissipation method on the fluid side of the heat dissipation structure is divided into traditional heat dissipation methods and new heat dissipation methods.
Traditional heat dissipation methods include flat heat sink heat dissipation, large channel water cooling, etc. Heat pipe heat dissipation and liquid metal heat dissipation. The advantages and disadvantages of various methods are summarized, and various heat dissipation methods are evaluated from the two indicators of heat flux density and temperature difference, and their application prospects in laser heat dissipation are discussed.
Usually, the heat sink of laser semiconductor has two methods: forced air volume and liquid cold plates. In the forced air-cooled heat sink, active component fans are used, which can improve the flow of hot air in the cabinet cavity. Skived fin is used. The heat sink of the process adopts materials with high thermal conductivity, which reduces the thermal resistance of conduction and avoids the increase of local
Thermal Solutions for Laser Equipment The power of semiconductor lasers continues to increase, and the heat dissipation problem caused by it has become a bottleneck restricting the development of semiconductor lasers. The increase in chip temperature causes the performance of lasers to decline. To keep the lasers with good characteristics under high power conditions, it is necessary to strengthen the heat dissipation of the laser chips.
By analyzing the influence of the laser chip temperature on various performance indicators of the laser, the importance of reducing the chip temperature to ensure the normal operation of the laser is explained. Since the convective heat transfer resistance on the fluid side plays a leading role in the total thermal resistance, the semiconductor laser is mainly analyzed.
The heat dissipation method on the fluid side of the heat dissipation structure is divided into traditional heat dissipation methods and new heat dissipation methods. Traditional heat dissipation methods include flat heat sink heat dissipation, large channel water cooling, etc. Heat pipe heat dissipation and liquid metal heat dissipation.
The advantages and disadvantages of various methods are summarized, and various heat dissipation methods are evaluated from the two indicators of heat flux density and temperature difference, and their application prospects in laser heat dissipation are discussed.
Usually, the heat sink of laser semiconductor has two methods: forced air volume and liquid cold plates. In the forced air-cooled heat sink, active component fans are used, which can improve the flow of hot air in the cabinet cavity. Skived fin is used. The heat sink of the process adopts materials with high thermal conductivity, which reduces the thermal resistance of conduction and avoids the increase of local temperature.
When the power of the laser module reaches a certain level, and also when the temperature control requirements are relatively strict, a heat dissipation method with a higher heat exchange effect is required. Therefore, the water cooling plate heat dissipation is the most common way. In indirect liquid cooling, semiconductor The laser heating element does not directly contact the liquid heat transfer medium.
Generally, this medium is water, which flows through the water cooling plate to the transfer water cooling plate, and then dissipates the heat into the air through the heat exchanger to achieve the purpose of cooling.