For high-power IGBTs, a stable and reliable junction temperature is very important. Generally speaking, the junction temperature standard is around 105 degrees. Considering the thermal resistance of the package and the thermal resistance of the thermal pad, theoretically the heat sink surface The temperature must be controlled at about 85 degrees, of course, the prerequisite is that the ambient temperature is 35 degrees. Under such conditions, it is generally easier to meet the conditions. Using high-power shovel fin radiators or high-density profile process radiators can meet the heat dissipation requirements. Of course, suitable fans are also very important.
However, for most industries, the temperature of IGBT needs to be controlled at about 50-60 degrees. In this case, higher requirements are placed on the selection of radiators. Therefore, general engineers will choose liquid-cooled plate radiators. The advantage of this heat dissipation method is that it is light in weight, and can take away a lot of heat by using the large specific heat capacity of the fluid, and then the copper tube heat exchanger dissipates heat into the air. This method is suitable for the needs of many precision devices, such as the medical industry, instruments equipment industry, etc.
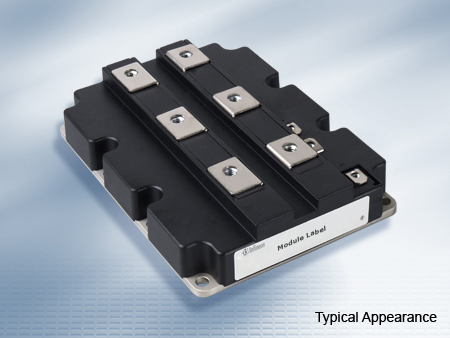
The following is an IGBT heat dissipation method of Infineon, and the design conditions are as follows:
- The operating power of IGBT is 3600W thermal power consumption,
- Using liquid cold plate system to dissipate heat
- The inlet water temperature is 20 degrees
- The ambient temperature is 20 degrees
- The maximum surface temperature of the water cooling plate is 60 degrees
The design scheme is to use an aluminum lqiuid cold plate. The aluminum plate is processed by CNC, and then a copper tube is embedded on it. The copper tube has a diameter of 8 mm and is bent at an angle of R15 to maximize the contact with more copper tubes under the IGBT. Waterways, that is, take away the greatest amount of heat. The gap between the heat pipe and the aluminum bottom plate is filled with epoxy resin to reduce thermal resistance. And the specific specifications are as follows:
- The product size is 280x250x20mm
- The material of the aluminum plate is aluminum 1060, and the thermal conductivity is 180W/m.k
- The material of the copper pipe is C1100, and the wall thickness is 1.25mm due to consideration of later processing
- Epoxy resin has high thermal conductivity, and the K value is 4.0 W/m.K
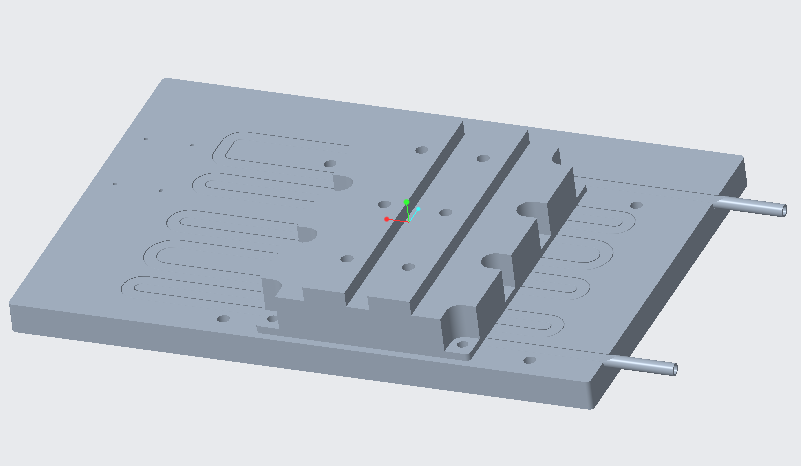
The design requirements:
•IGBT thermal power 3600w;
•Al6063 Material for Al base
•Liquid cold plate with epoxy bonding process
•Input flow rate 10L/Min
•Inlet water Tem 20 ℃
•Environment 20℃
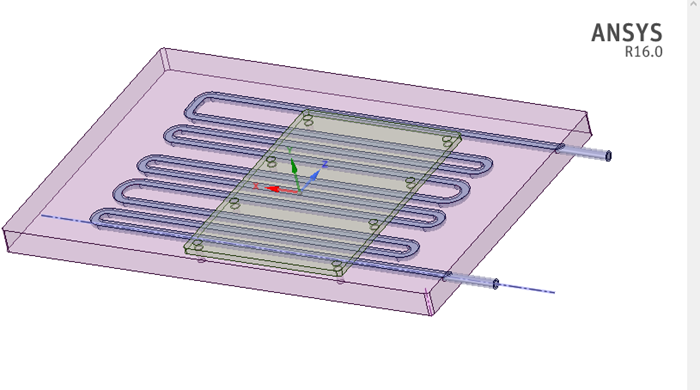
Basic Parameter Setting
•Ambient temperature 20 ℃
•Thermal radiation is not considered
•Turbulent flow regime
•Operating pressure 101325N/m2 on Natural convection
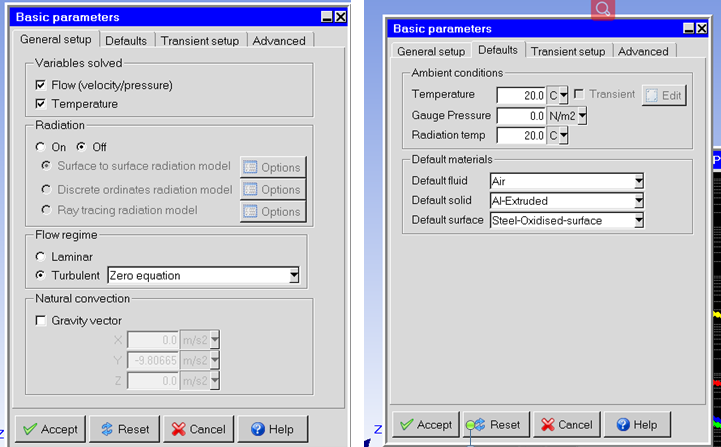
•The number of meshes is 1135933
•Set uniform mesh params
•Mesh assemblies separately
•Allow multi-level meshing
•Allow minimum gap changes
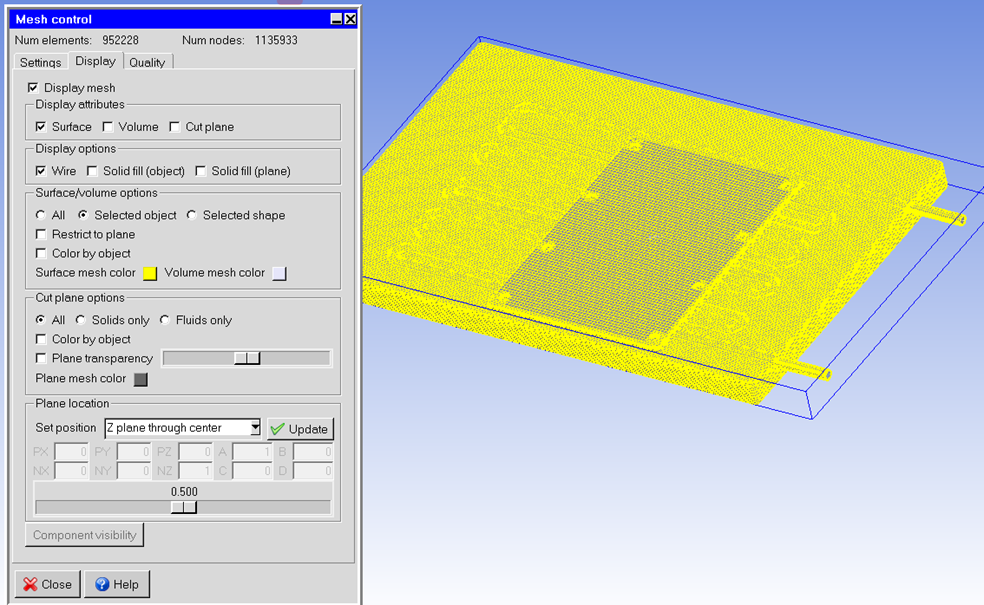
Run the solution and get the function curves
•The running step is 1000, and the actual function converges to 150 steps
•The convergence factor flow value is 1xe-5(0.00001)

The maximum surface temperature of liquid cold plate is 49.5 ℃
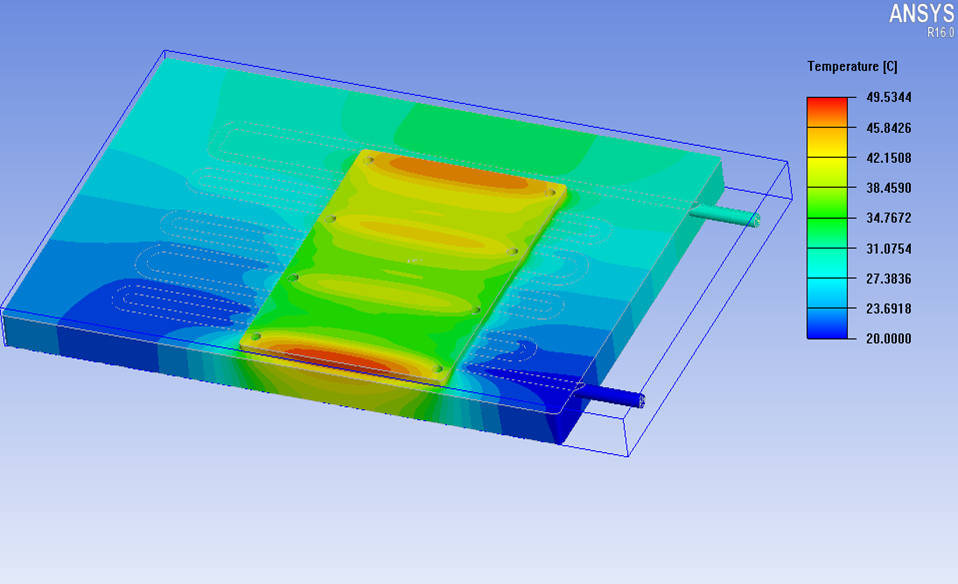
Water Speed distribution
•The maximum speed is 14.69m/s
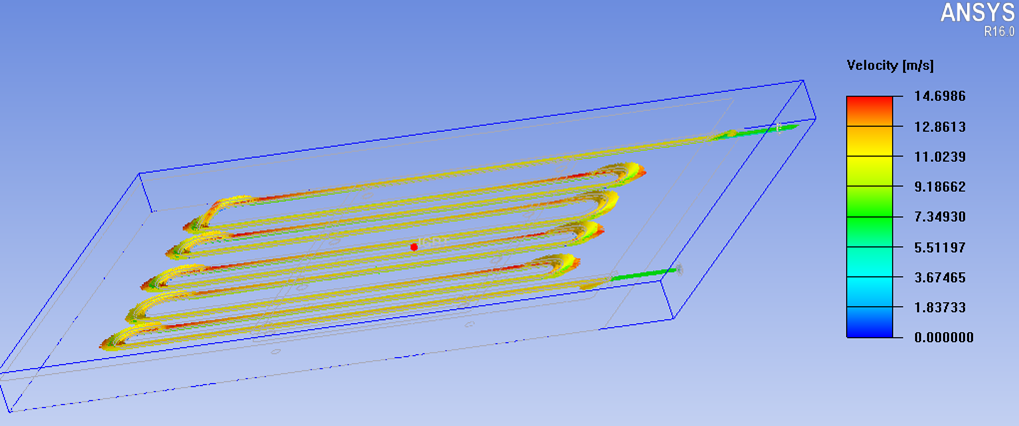
•Water pressure distribution
• The maximum differential pressure is 1552780N/m2
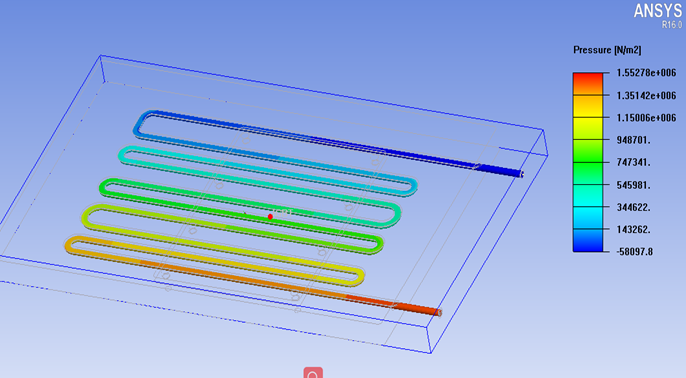
The results:
•Used the simple model method, the result will be different from the actual module.
•The heat sink surface Max temperature is 49.5℃
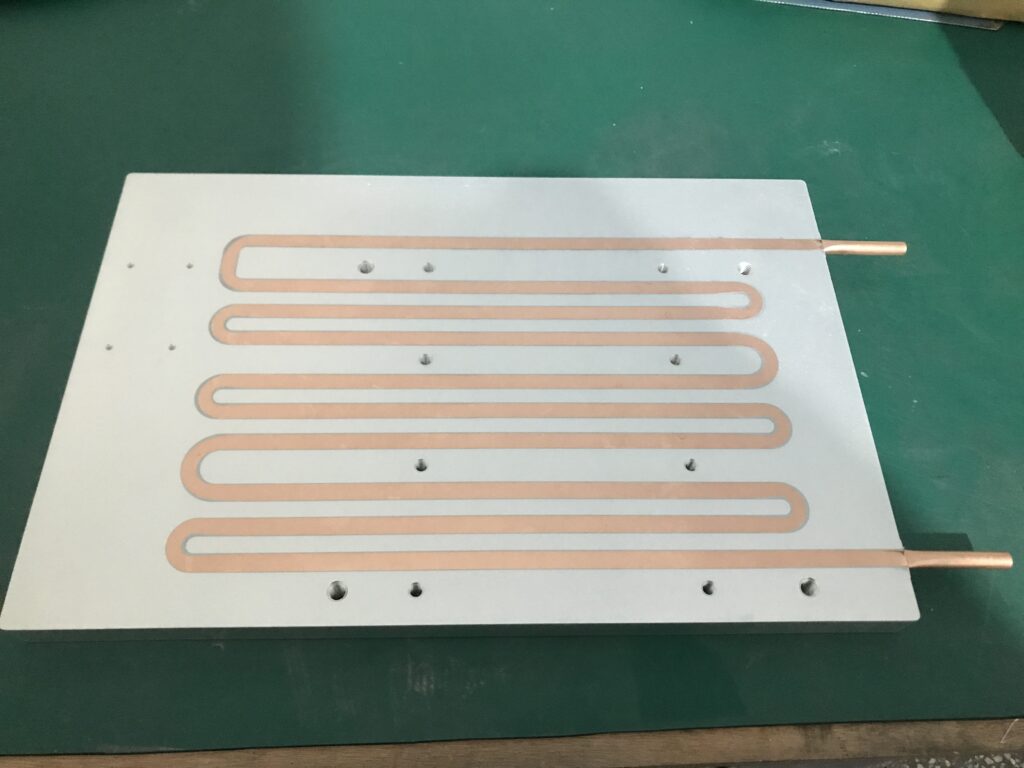
The actual test meets the design requirements, and the surface treatment of the liquid plate is chromate coating.