Friction Stir Welding Cold Plate
Custom friction stir welding cold plate with YT Thermal.
The friction stir welding method is the same as conventional friction welding. Friction stir welding also uses friction heat and plastic deformation heat as welding heat sources.
FSW Cold Plate Solution
Liquid cold plate
Customized thermal solutions of FSW process
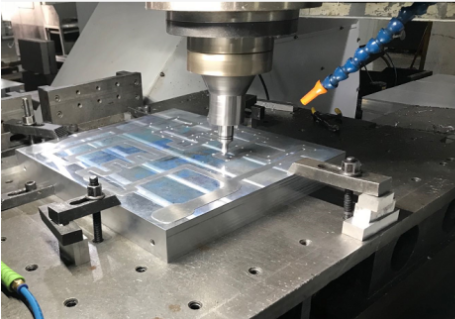
The friction stir welding method is the same as conventional friction welding. Friction stir welding also uses friction heat and plastic deformation heat as welding heat sources. The difference is that the welding process of friction stir welding is that a welding pin of a cylinder or other shape (such as a threaded cylinder) is inserted into the joint of the workpiece, and the high-speed rotation of the welding head is used to make it and welding.
The workpiece material rubs, so that the temperature of the material at the connection part increases and softens. At the same time, the material is subjected to friction stir to complete the welding.
During the welding process, the workpiece should be rigidly fixed on the back pad, the welding head rotates at a high speed, and the edge moves relative to the workpiece along the seam of the workpiece.
The protruding section of the welding head protrudes into the material for friction and stirring, and the shoulder of the welding head rubs against the surface of the workpiece to generate heat, and is used to prevent the overflow of the plastic material, and at the same time, it can remove the oxide film on the surface.
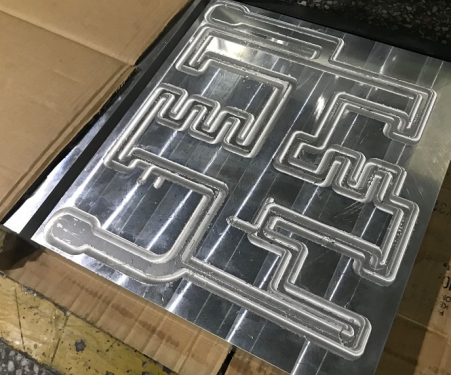
During the welding process, the stirring needle extends into the seam of the workpiece while rotating, and the frictional heat between the rotating stirring head (mainly the shaft shoulder) and the workpiece causes strong plastic deformation of the material in front of the welding head, and then with the With the movement of the welding head, the highly plastically deformed material is gradually deposited behind the mixing head, This results in a friction stir welding seam.
The requirements of friction stir welding on equipment are not high. The most basic requirements are the rotational movement of the welding head and the relative movement of the workpiece. Even a milling machine can easily meet the requirements of small flat plate butt welding. But the rigidity of welding equipment and fixtures is extremely important.
The stirring head is generally made of tool steel, and the length of the welding head is generally slightly shorter than the required welding depth. Using the CNC process to process the water channel, and then using the stir welding process to cover the cover plate of the water-cooled plate on it, after friction welding, it can be made into a water-cooled plate with very good reliability. Take away the heat of the laser module, so as to reduce the temperature..
Cold plate material: Al6063/6061/1060 /Copper C1100
Copper tube: C1100/Al 1100/Stainless steel
Finishing: Washing or Chromate coating
Testing: Helium test or water pressure test
Application: IGBT, Laser module
Size: Customized Size
Service: OEM, CNC machining parts manufacturer
Sample Lead Time: 15~20 days
Quality Certification: ISO9001:2015
QC control: sampling inspection, full inspection
Surface roughness: 0.2 ra
Packaging Detailscartons or as request
Port: HK/Shenzhen
Design Process:
Customer’s input (drawings or asked) – Design proposal – Do the simulation
– Make the prototype – Verification – Customer validation – Tooling fabrication
– Pre series production – Acceptance Validation – Mass prodcution
Standard specification dimensions are as follows:
(Length X Width X HighX Fin thickness X Fin Spacing,Unit mm)