Cold Forged Heat Sink
Cold forged heat sink is a type of heat sink than using cold forging process. Cold forging is to use the principle of plastic deformation of metal materials. At room temperature, the metal is put into the mold cavity that has been processed in advance.
Cold forged heat sink solutions
Heat Sinks
Customized Thermal Solutions of cold forged heat sinks
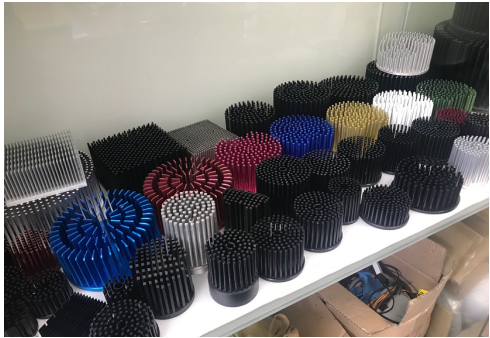
The definition of cold forged process
Cold forging is to use the principle of plastic deformation of metal materials. At room temperature, the metal is put into the mold cavity that has been processed in advance, and then the mold is put into the mold cavity of the cold forging machine. Under the action of a strong unit extrusion and a certain speed, the metal is forced to plasticize and deform in the mold cavity to achieve the required shape.
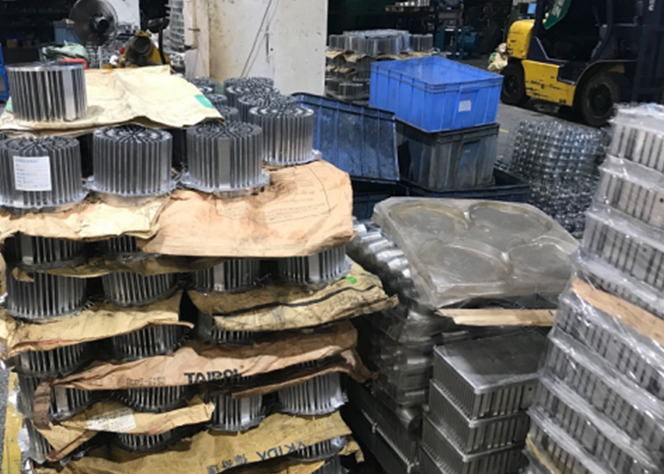
Under normal circumstances, the general radiator is AL1060 model, and the copper material is generally C1100. The shape of the radiator fin can be circular or has a certain thickness. Usually, the minimum ratio of fin thickness and spacing is 1:3.5, and the height is 1:3.5. 28 times the thickness, that is to say, the maximum height of the heat sink fin with a thickness of 1mm is 28mm.

The cold forged or cold extruded heat sink should be as axially symmetrical as possible, and the thickness and spacing of the fins should be designed in proportion to ensure that the metal flows evenly during the forming process
The draft angle and fillet radius of the radiator fin: during cold forging, an ejector is generally installed, and the draft angle is about 0 ~ 3. The fillet radius is based on R2. Pay special attention to the fillet during cold forging. Too large will affect the forming
Standard specification dimensions of cold forged heat sink are as follows:
(Length X Width X HighX Fin thickness X Fin Spacing,Unit mm)
650x1200x90x1.2×3.6 / 650x1000x90x1.2×3.6 / 650x800x90x1.2×3.6 / 650x650x90x1.2×3.6