Brazed Cold Plate
Customized Brazed cold plate for IGBT cooling. Electronic components in special environments need a heat dissipation solution with low thermal resistance.
Brazed Cold Plate Solutions
Liquid cold plate
Customized thermal solutions of Brazing process
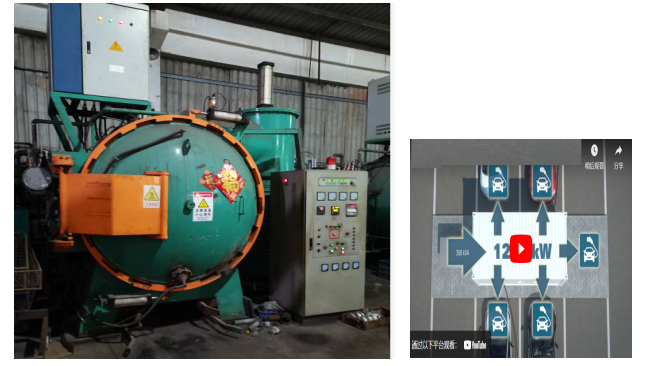
Generally, there are high-density folded fins inside the brazed water-cooling plate, so that when the fluid passes through this high-density heat, the heat is exchanged quickly and the heat is quickly taken away. Under normal circumstances, this heat dissipation efficiency is relatively high, and the reliability is relatively good. It is usually used by many laser module companies.
Generally, the material of this water-cooling plate can be flexible and changeable, which can be copper material with high thermal conductivity, or aluminum material. Under normal circumstances, the brazing process of copper material is used, which is generally carried out in a vacuum brazing furnace, and the temperature will reach about 750-850 degrees.
Under the protection of vacuum and nitrogen, the components of the water-cooled plate and the brazing paste are welded together. The aluminum material has a relatively low temperature, generally at a temperature of about 580-710 degrees, so that the cover plate of the water-cooled plate and the inner fin are welded together.
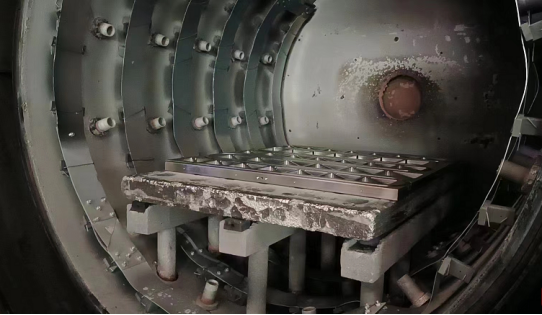
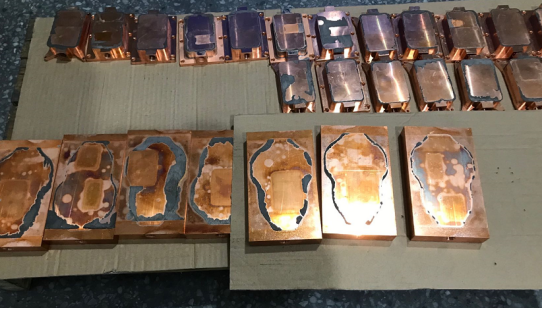
Cold plate material: Al6063/6061/1060 /Copper C1100
Copper tube: C1100/Al 1100/Stainless steel
Finishing: Washing or Chromate coating
Testing: Helium test or water pressure test
Application: IGBT,Laser module
Size: Customized Size
Service: OEM, CNC machining parts manufacturer
Sample Lead Time: 15~20 days
Quality Certification: ISO9001:2015
QC control: sampling inspection, full inspection
Surface roughness: 0.2 ra
Packaging Detailscartons or as request
Port: HK/Shenzhen
Design Process:
Customer’s input (drawings or asked) – Design proposal – Do the simulation
– Make the prototype – Verification – Customer validation-Tooling fabrication
– Pre series production – Acceptance Validation – Mass prodcution
Standard specification dimensions are as follows:
(Length X Width X HighX Fin thickness X Fin Spacing,Unit mm)
650x1200x90x1.2×3.6 / 650x1000x90x1.2×3.6 / 650x800x90x1.2×3.6 / 650x650x90x1.2×3.6