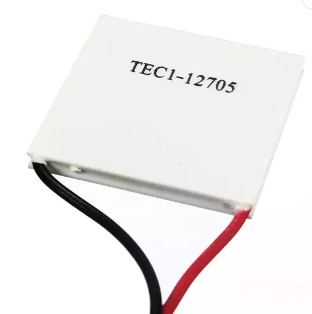
Analytical chemists use reagents to detect the presence or absence of certain substances, or to test for the occurrence of specific reactions; laboratory and medical technicians use reagents to cause chemical or biological reactions to measure or identify target substances; biotechnologists use antibodies, model organisms (model organism), oligomer (oligomer), and specific cell lines are considered reagents for identifying and manipulating cellular material. These reagents, especially those used by biotechnologists, have a very narrow working temperature window and require refrigeration or freezing.
When stored at room temperature, temperature-sensitive reagents degrade and can become contaminated with microbial growth, compromising test integrity. Without proper and precise refrigeration, most reagents will deteriorate within hours. Additionally, some reagents can be negatively affected if stored at too low a temperature or subjected to multiple freeze-thaw cycles. Stabilization at precise temperatures below ambient, and close monitoring of the temperature, is critical to extending reagent life, reducing replacement costs, and ensuring the accuracy and reliability of laboratory and medical testing.
Active thermoelectric coolers (TECs) provide precise temperature control and are ideal for thermal management of reagents. Thermoelectric coolers are a more efficient, cost-effective and reliable method of temperature control than other thermal management technologies. Governmental organizations have banned the use of many refrigerants that are essential to other thermal management technologies, so the refrigerant ban has also affected the design of reagent storage equipment. Thermoelectric coolers, which do not require refrigerants, provide a more environmentally friendly solution for temperature control of reagent storage.
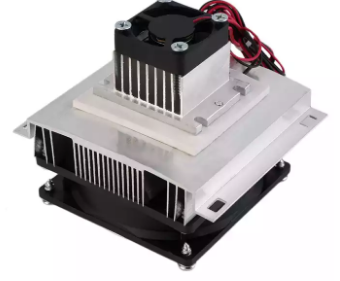
Application overview
Due to the wide variety of reagents in the medical industry, each reagent has different requirements for storage temperature, so there is no general temperature storage standard in the industry. According to different reagent types and specific storage time requirements, laboratory and medical reagent storage systems also require different specifications.
Depending on the temperature control range, reagent storage systems are generally divided into five types:
• Low temperature freezer → -150ºC ~ -190ºC
• ULT freezer → – 85ºC
• Standard freezer → – 20ºC
• Refrigerated → 2ºC ~ 8ºC
• Room temperature → 15ºC ~ 27ºC
In this application note we will focus on refrigeration system requirements and refrigeration solutions for most reagents that need to be refrigerated at 2ºC.
Refrigeration temperature ranges from 2ºC to 8ºC, which is most suitable for short-term storage of commonly used biological reagents, including some enzymes and antibodies. Within this temperature range, most reagent samples experience small but acceptable temperature fluctuations. At a room temperature of 20 to 30°C, the standard reagent storage system is capable of maintaining the temperature control of the reagent barrels at 4°C to 6°C, with refrigeration capacity requirements ranging from 30 to 50W. More advanced medical storage refrigerators, which can be used to store extremely temperature-sensitive reagents, must maintain the temperature at the thermostat set point within ±2ºC.
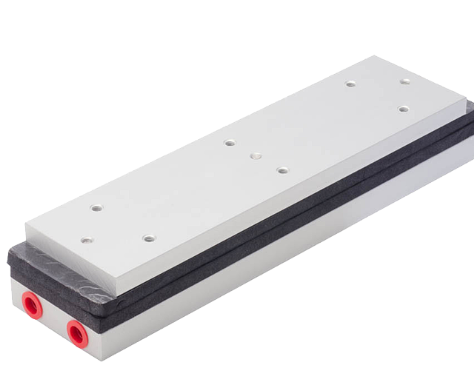
Application challenges
In addition to precise temperature control, reagent refrigeration designs have SWaP (size, weight, and power) requirements and other challenges, including reducing operating noise, airflow management, condensation mitigation, and temperature alarms. Meeting all of these code requirements without using restricted refrigerants can present challenges for thermal design engineers.
Manufacturers of medical instruments and diagnostic equipment need to reduce the size of laboratory equipment according to market requirements. The miniaturization of reagent storage devices can free up more valuable laboratory space, which prompts engineers to integrate more functions into a more compact space Inside. Space constraints within reagent storage systems require a thermal control unit with a compact form factor to maximize storage capacity. Concentrating electronics into a smaller footprint increases heat flux density, and this excess heat must be efficiently managed and dissipated to satisfy the conflicting triad of increased performance, reduced power consumption, and quieter operation. requirements, all of which need to be implemented in a smaller design.
Since space is at a premium, mounting location and orientation often play a significant role in the choice of thermal management solution. Compressor-based systems must be installed vertically to operate properly, whereas thermoelectric devices can be installed in any orientation. Mounting orientation also affects airflow. The path of incoming and outgoing air must be considered to maximize cooling and/or heating performance.
In reagent storage equipment, thermal management systems need to provide not only temperature stability but also condensation protection. When temperatures drop below the dew point, moisture can form on cold surfaces and can seep into electronic equipment, causing it to degrade and possibly eventually fail. Good design implementation requires a cooling solution that prevents moisture ingress, combined with the use of well-designed isolation materials.
Many laboratories regularly record the temperature of reagent storage rooms to ensure reagent integrity. While it is important to record the temperature, it is more valuable to determine whether the temperature of the storage room is outside the set temperature range. As a result, many medical refrigeration systems have temperature alarms that allow technicians to take quick action to protect stored reagents in the event of temperature excursions.
New environmental regulations, especially in Europe, have banned the use of certain refrigerants. Older compressor-based systems use HFC refrigerants that can contribute to global warming, including R134a and R404A. The ban by government organizations has forced many manufacturers of compressor-based refrigerators to switch to natural refrigerants. Modern compressor-based systems are currently available with various natural refrigerants: R744 (carbon dioxide), R717 (ammonia), R290 (propane), R600a (isobutylene) and R1270 (propylene), among others. However, each natural refrigerant has its design challenges, such as high pressure, high toxicity, flammability, asphyxiation, and relatively poor performance. The flammability of some natural refrigerants makes them dangerous to transport, prompting manufacturers to seek other methods of temperature control, such as thermoelectric technology-based refrigeration solutions.
Thermoelectric Cooling Solutions
Thermoelectric coolers are solid-state heat pump devices that transfer heat through the thermoelectric effect. During operation, a direct current is passed through the thermoelectric cooler, which creates a temperature difference across the module. One side of a thermoelectric cooler becomes cold (heat absorption) while the other side becomes hot (heat dissipation). Thermoelectric coolers are usually connected to a forced convection heat sink on the cold side and absorb heat from inside the cabinet, while the hot side heat sink rejects heat to the surrounding environment. Thermoelectric coolers can also heat the inside of the cabinet by reversing the polarity of the device. This dual function coupled with the control circuitry enables precise temperature control in one unit.
Compared to other technologies such as compressor-based refrigeration systems, thermoelectric coolers are energy-efficient, stable, compact, and reliable devices that provide accurate temperature control. In addition, thermoelectric coolers are environmentally friendly devices that do not require any refrigerant to dissipate heat.
Thermoelectric coolers feature solid-state construction with no moving parts for reliable operation at low power, without noise, and in a small footprint. This solid-state operation gives designers increased integration flexibility since thermoelectric devices can be mounted in any orientation.
For YTthermal system solutions, we can design solutions with the same power requirements for customers, and their cost performance is the highest. We can provide the most diverse product portfolio in the industry, including active thermoelectric cooling chips and components to temperature controllers and liquid refrigeration systems. With unparalleled thermal management expertise, our engineers are able to solve complex thermal management and temperature control problems using advanced thermal simulation and thermal management techniques.